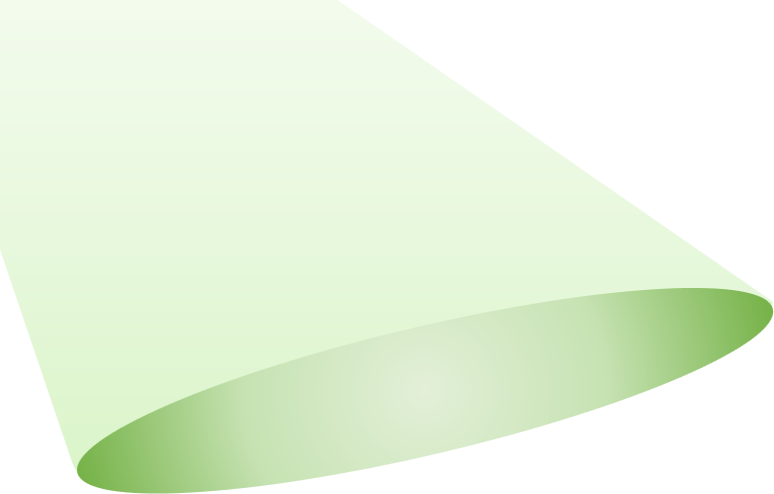
SERVICE SPOTLIGHT
Walk the Talk: Five Steps to a Sustainable Supply Chain Strategy
By Aditi Busgeeth, Senior Analyst, Third Economy, January 2024
Last week, we discussed why integrating ESG considerations into your supply chain is more important than ever. But how do you execute a sustainable procurement program? We highlight the key steps below.
Source: Third Economy analysis
- Identify the priority ESG issues
Time and money are limited, so determine what the critical ESG topics are for your company. A materiality assessment is a useful exercise and can shape your entire ESG strategy, even beyond supply chain aspects.
Alternatively, analyze peer ESG disclosures, popular third-party activism, and common product certifications to determine the hot-button issues for your customers. These will vary greatly depending on your industry. For example, avoiding conflict minerals may be a top priority for electronics manufacturers but may be less relevant for a restaurant chain.
TIP: Don’t overlook feedback from your employees on what ESG topics are priorities. It’s important to identify and address the “blind spots” of the company, and those who work directly with the suppliers or investors are key sources of firsthand information.
Case Study: Consumer Company Integrates ESG Factors into Procurement Strategy
The Situation: A large consumer company (the “Company”) in the United States recently received public inquiries on its climate strategy and supply chain practices, such as its transition to cage-free eggs.
The Ask: Recognizing these stakeholder inquiries as an opportunity to advance their oversight and approach to their supply chain, the Company reached out to Third Economy for guidance on how to prioritize and integrate ESG into its procurement strategy.
The Solution: Third Economy conducted a comprehensive benchmarking exercise that examined industry expectations, best practices from six peer companies, and consumer trends to recommend the next steps to the Company. In close collaboration with the Company’s procurement team, Third Economy suggested key performance indicators (KPIs) and reputable tools that the company could leverage as it built out its capabilities and responded to stakeholder questions.
We also conducted a Scope 3 greenhouse gas materiality screening to help the Company identify the most important sources of emissions in its upstream and downstream value chains.
- Find out what you know (and what you don't know) about your suppliers
After you identify your company’s key issues, you should build profiles of your suppliers as a part of a thorough supplier risk assessment. Example questions you might ask for each supplier:
-
- Is the supplier in a high-risk geographic area, where it is more likely to be affected by labor instability, political unrest, or corruption?
- How dependent is your company on the supplier? If the supplier was non-compliant with your expectations, would you be able to pivot to other vendors?
- What is the supplier’s track record with safety, quality, and environmental issues?
- What kind of workforce does the supplier have? For example, does it rely heavily on migrant labor?
- Does the supplier have grievance mechanisms to receive and properly address worker concerns?
TIP: We also recommend expanding your risk assessment to include your lower-tier suppliers.
Many companies complete risk assessments only for their Tier 1 suppliers, who manufacture or provide services directly to the company. However, a 2020 Harvard Business Review analysis found that lower-tier suppliers are “unquestionably the riskiest members of the supply chain.” Faced with less scrutiny, accountability, and resources than Tier 1 suppliers, lower-tier suppliers frequently have insufficient environmental, health, and safety programs.
- Set expectations with suppliers
As your organization agrees on how suppliers should handle key ESG issues, it’s a good idea to formalize these expectations through documents such as a vendor code of conduct, a human rights policy, and an environmental policy. Communicate these expectations with our suppliers and incorporate them into your contracts with suppliers.
Establishing distinct ownership within your organization for each supplier relationship is crucial. A relationship manager helps set the expectations for both sides, oversees quality control, addresses issues promptly, and promotes regular and transparent communication between the supplier and your company.
- Follow through with regular supplier monitoring and training
Consistent supplier engagement is vital to ensure that safe and equitable working conditions are maintained, climate promises are kept, and quality products are made. Your organization should organize regular, onsite audits (ideally unannounced) of manufacturing sites. After the audit, follow through to make sure any non-compliances are addressed quickly.
Invest in relationships with suppliers and provide capability-building resources. For example, your company might offer supplemental health and safety training or highlight diverse suppliers on your website. Another approach is to share information about problems happening upstream and downstream of the supplier’s operations, which improves communication and promotes collaboration during disruptions.
- Report your progress transparently
Of course, this level of transparency may differ where you are in your ESG journey. Generally, a company can start by publishing its supply chain governance documents, such as its vendor code of conduct and its human rights statement.
As your supplier ESG strategy matures, consider disclosing your KPIs publicly, such as relevant Scope 3 greenhouse gas emissions, onsite audit results, and supplier diversity metrics. Target, for example, shares many metrics for its supply chain responsibility program, such as spending with diverse suppliers, the percentage of suppliers screened for social impacts, and the average number of health and safety issues per audit.
Begin to set goals and implement initiatives to move your supplier ESG strategy beyond the foundational phase. For example, a company may commit to circularity initiatives or implement a zero-tolerance policy for the use of child slavery.
Working Smarter, Not Harder: Resources to Get Started
There are plenty of resources available to help you and your organization to develop and deploy a supplier ESG strategy:
- EcoVadis – assesses companies’ sustainability programs in four categories: Environment, Labor and Human Rights, Ethics, and Sustainable Procurement. EcoVadis allows procurement professionals to gather information on their suppliers’ sustainability performance suppliers and share details about their own company’s program with stakeholders.
- OECD’s Four Keys to Resilient Supply Chains – Created for policymakers in the wake of COVID-19, this toolkit includes firm-level strategies for companies to build resilience and trust in their supply chains.
- ISO 2600:2010 standard – Global standard that focuses on social responsibility, including how a company can implement and promote socially responsible behavior throughout its organization and within its sphere of influence. Note that this is a guidance standard, not a compliance standard, so no certification is available.
But Wait...There's More
Do you want expert guidance in creating a customized sustainable procurement strategy? Get in touch with the Third Economy team. We can help you build an ESG program that elevates your business and connects profit with purpose. Let’s shape a sustainable future together.
Disclaimer: The information provided does not, and is not intended to, constitute legal advice; instead, all information, content, and materials available are for general informational purposes only.